Roughing End Mill Depth Of Cut
This is because the cutting resistance is reduced because the chips are broken into short lengths by the wavy cutting edges. This increases the tool engagement angle to nearly 180º at a 50% rdoc, resulting in significant additional cutting forces, increased likelihood for chatter, tool

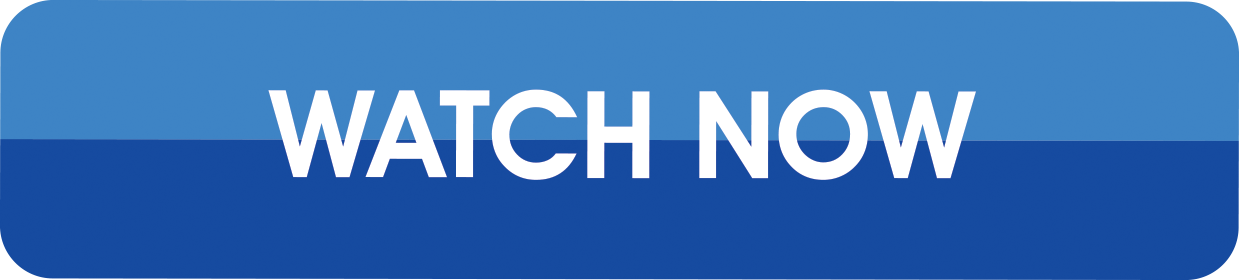
Material specific feed rates and radial stepovers dictate flute count, with most optimized roughing operations using end mills with between five and nine flutes.


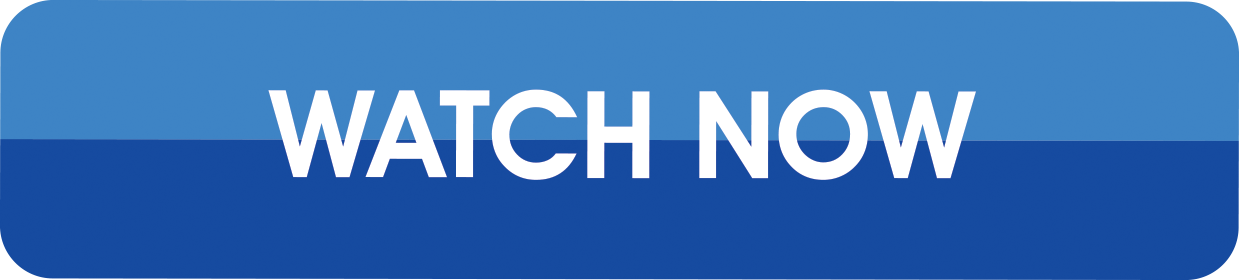
Roughing end mill depth of cut. Cobalt roughing end mills are designed to withstand heat and abrasion and can be run at higher production rates without sacrificing tool life. This spreads wear evenly across the cutting edge, dissipates heat, and reduces the chance of tool failure. The depth of cut plays a vital role in optimizing roughing.
2) the irregular helix flute end mill has a large effect on controlling vibration when compared to standard end mills. Because the cutting pressure was only 2/3's Standard depths of cuts for roughing end mills can be set at a larger value than ordinary type end mills.
After rough cut, a finish cut or finishing pass is carried out to improve surface finish, dimensional accuracy and tolerance level. Beyond that point, axial cutting pressures cause end mill deflection and hamper good chip formation. This step is called rough cut or roughing pass.
Widia hanita 5329388 series eccentric rougher 6 flute inch roughing & finishing end mill, 76.2 mm max depth of cut, 31.75 mm dia shank This setting will impact rct calculations as well. For smaller mills whose spindle won’t exceed 6000 rpm that will be cutting aluminum, i typically recommend hss for endmills larger than 1/2″ diameter and carbide for smaller endmills.
Mrr = axial depth of cut * radial depth of cut * feed rate (all values in inches or inches per minute for feed rate) this formula yields the number of cubic inches per minute your cutting tool is removing. Side loading is dramatically reduced with lower helix angles, making it easier to mill thin walls. And axial depth of cut (adoc), the distance a tool engages a workpiece along its centerline, are the backbones of machining.
Inches per revolution (ipr) — feed rate of the cutter for each revolution of the cutter. The tooth design allows for little to no vibration, but leaves a rougher finish. In the inch system, the feed rate of the cutter can be calculated for each revolution of the cutter.
The roughing cut i divided the tool by 80 for the chip load. This saves a lot of cost on the larger endmills (which you might prefer be indexable and using carbide inserts anyway) but keeps the rigidity up on the smaller endmills. End mill diameter should measure half the cutting length/ depth of cut;
Light roughing <50% radial depth of cut tea tea match an end mill radius to that of the inside corner being machined and execute a 90º turn in cut direction. The tooth design and flute construction minimizes deflection and maximizes chip ejection. Higher feed rate and depth of cut are employed for this step so that high stock removal rate is obtained.
In 2xd and the entire edge length of the milling cutter, the effect of one pass is the best. Hem is a roughing technique that uses a lower radial depth of cut (rdoc) and a higher axial depth of cut (adoc). Roughing end mills, also known as hog mills, are used to quickly remove large amounts of material during heavier operations.
This results in lower cutting pressures at a given radial depth of cut. I was wondering what others normally consider maximum depth of cut ratio to diameter of end mill with a roughing end mill milling cast iron medium hardness ?? End mill:φ10 4flutes rotation:2,550min-1 feed:1,500mm/min cut depth:aa10mm ar10mm slotting material:skd11(220hb) dry(no air blow) 10mm
Now here’s the last piece: Here very low feed rate and. Roughing end mills roughing cuts are generally for preparing the surface before the.
Normally i would use a depth of cut of.31 to.625 with a.625 dia roughing end mill for a full width slot feeding straight across g1 Roughing end mill, short cut length, 6 flute,. However, if the rigidity of
While traditional roughing is occasionally necessary or optimal, it is generally inferior to high efficiency milling (hem). Roughing end mills have scallops on the cutting edges, which cause the chips to break into smaller segments. End mills coolstar 1) if the depth of cut is shallow, the revolution and feed rate can be increased.
It cannot provide good surface finish and close tolerance. The tougher the material the shallower the cut. Corner radius end mills have a rounded cutting edge and are used where a specific radius size is required.
Volumes of material can be. End mill was average length with 1.5 loc flute for 5/8 dia end mill. Their extreme hardness means they are brittle, so a highly rigid setup, such as a cnc machine, is necessary to prevent the end mill from breaking.
Depth of cut (doc) — the depth of cut of the end mill into the part surface axially. The machining time spent roughing your workpiece is mostly determined by material removal rate. Radial depth of cut (rdoc), the distance a tool is stepping over into a workpiece;
With cnc milling, it is measured in the z axis direction. A shallower radial span makes the cutting depth deeper, while a larger span value generates more heat, and requires a shallower cutting depth to achieve the same metal removal rate. They are designed to remove large amounts of material quickly and more efficiently than standard end mills.

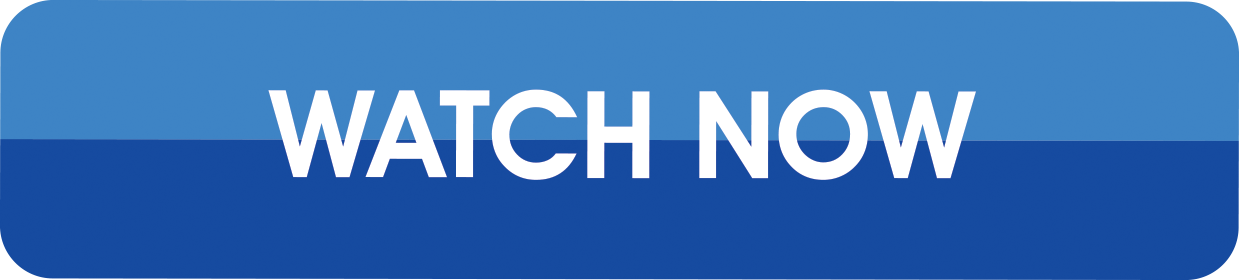

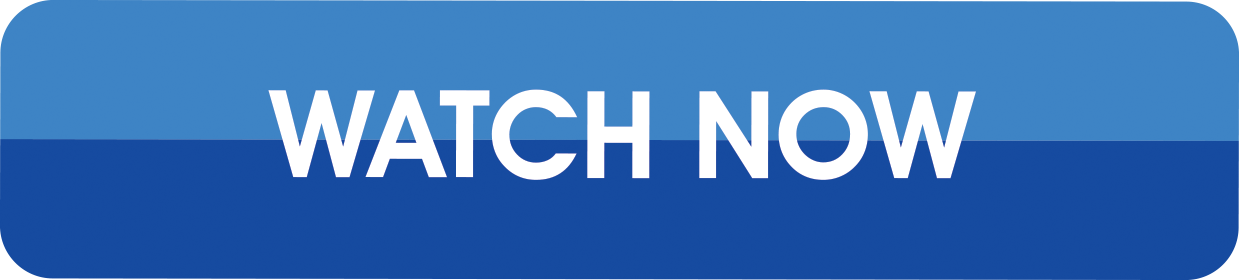

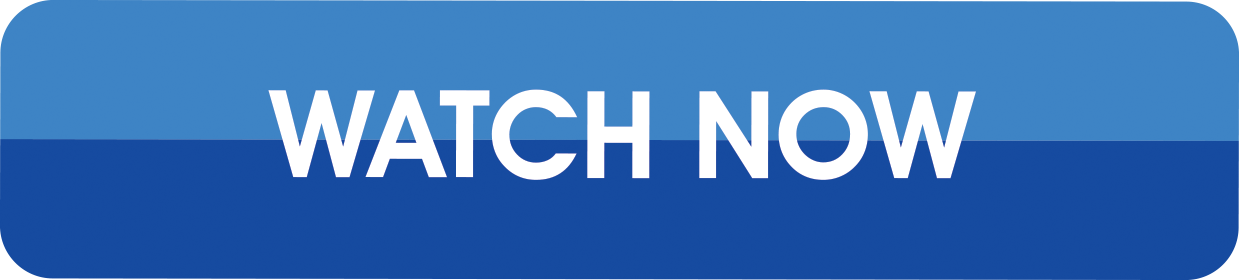
0 Response to "Roughing End Mill Depth Of Cut"
Post a Comment